The fabrication of our products is a meticulously planned process that combines advanced technology with expertise and dedication to quality. CSUB has a solid reputation for delivering products of the highest standard to a variety of industries, and the fabrication processes are core components of this success.
The fabrication process begins with precise design and modelling of components using advanced CAD technology. Materials are carefully selected to ensure optimal strength, durability, and performance
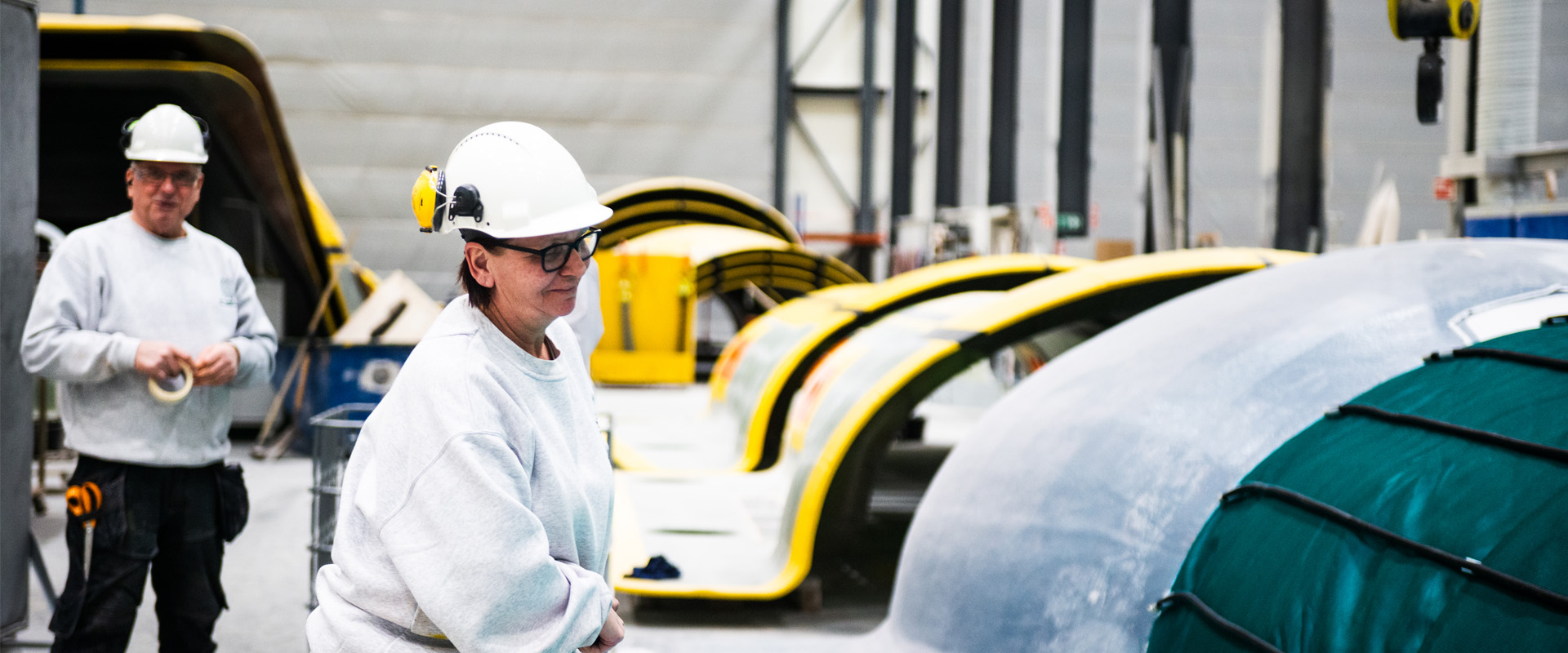
Fabrication
The Process – Vacuum infusion
Vacuum infusion is a process used in composite manufacturing where resin is drawn into a dry fiber reinforcement through the application of vacuum pressure.
- Preparation: Dry reinforcement materials, such as fiberglass or carbon fiber, are laid out in a mold. This mold is then sealed with a vacuum bagging film.
- Resin Infusion: A vacuum is applied to the mold, removing air and gases from the space between the reinforcement and the mold. This creates a pressure differential that allows resin to be drawn into the mold, saturating the reinforcement.
- Curing: Once the mold is fully infused with resin, it is cured using heat or chemical catalysts. This solidifies the resin, bonding the reinforcement materials together and forming the final composite part.
Advantages:
- Uniformity: The vacuum infusion process ensures uniform resin distribution throughout the part, minimizing voids and inconsistencies. This leads to parts with consistent mechanical properties and improved performance.
- Reduced emissions: Compared to traditional wet lay-up methods, vacuum infusion produces fewer emissions and waste. It is a cleaner and more environmentally friendly manufacturing process.
- High fiber volume fraction: Vacuum infusion allows for a high fiber volume fraction, meaning a greater proportion of fibers compared to resin in the composite. This results in parts with excellent strength-to-weight ratios.
- Complex Shapes: Vacuum infusion can be used to manufacture parts with complex shapes and intricate geometries. The process easily conforms to the contours of the mold, allowing for the production of highly customized components.
- Traceability: Full traceability and documentation of material and process
- Cost effiency: While vacuum infusion may require initial investment in equipment and setup, it can lead to cost savings in the long run due to reduced material waste, improved process efficiency and lower labor costs.
Overall, vacuum infusion is a versatile and efficient manufacturing process that offers numerous advantages in terms of part quality, performance, and environmental impact.
Quality Management
For production quality control, CSUB have developed Quality Control Documents/Check lists to cover the following:
- Receipt of materials – all raw materials and CPI to be checked upon receipt
- Glass fibre layup – full traceability records for raw materials
- Full traceability records for lay up and resin injection operation including temperature/ humidity etc.
- Test procedures and logs
- Final Inspection
CSUB is Qualified in the Achilles Joint Qualification System for suppliers tothe Oil Industry in Norway and Denmark. Our Achilles ID is 29130.
Want to know more about Glass fiber reinforced polymer (GRP) for Subsea structures ?